Ceramic Magnets
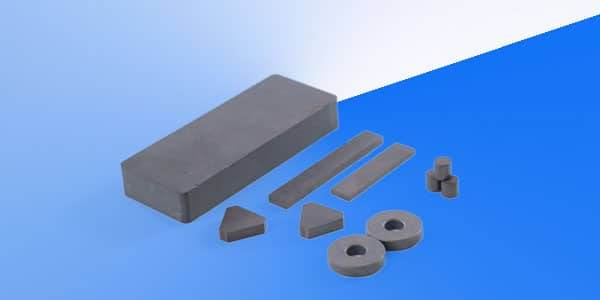
Ceramic Wholesale Supplier
AZ Industries carries a wide range of shapes and sizes of ceramic magnets. Our ceramic (ferrite) magnets have rectangular blocks from small to large, cylinders, rings, discs, triangles, and special shapes. As one of the top magnet suppliers and custom magnet manufacturers in America, we offer some of the shortest lead times for custom machined magnets.
We have many standard sizes available off the shelf and special sizes can be made upon request. Ceramic, or ferrite, magnets are made by the pressing and sintering of a powdered mixture of strontium and iron oxide. They are the most widely used magnets today. Ceramic is inexpensive and corrosion resistant, but cannot withstand impact or flexing as they will chip and crack due to their hard and brittle nature.
No surface treatments are necessary for ferrite magnets. However, a thin film of fine magnet powder on the surface is common and a coating may be used for cleanliness purposes. Common grades of ceramic are 1, 5 and 8 and can be found in the form of discs, rings, blocks, cylinders, and sometimes arcs.
Attributes of Ceramic Magnets
Ceramic Magnet Applications Include
Ceramic or Ferrite Magnet Machining, Handling, and Limitations
Brittleness
It is important to note that Ceramic (or sometimes referred to as Ferrite) Magnets are very hard and are also quite brittle. This makes these magnets subject to chipping or breakage when dropped on a hard surface. If you allow two ceramic magnets to snap together, this will most likely result in several sharp pieces. Ceramic magnets are not flexible, will not withstand impact and would be a poor choice for structural purposes.
Ceramic magnets are chemically inert and non-conductive which offer advantages in applications requiring these attributes. We manufacture magnetic assemblies made with ceramic magnets, but because of the brittleness, we typically magnetize ceramic assemblies after the product is assembled.
Temperatures
Ceramic Magnets exhibit temperature limitations with a maximum operating temperature at 800°C. Elevated temperatures result in magnetic strength loss, but strength recovers when the material returns to room temperature. Temperatures above 450°C will require remagnetization. When using these magnets in applications involving cold temperatures of -20°C or below, please note that permanent loss of magnetic strength may result.
Machining
Because of the properties of ceramic magnets, most of the machining has to be done with diamond tooling. It is very similar to cutting ceramic tile…slow and steady is the rule of thumb to avoid large chipping. Small chipping will occur so most of the time ceramic magnets must be cut oversized and then ground to the customer’s tolerances.